Innovation in the Solar PV Industry
The processes for inspecting solar PV systems has changed greatly over the last few years. Recently the use of a drone (UAV) or manned aircraft (plane) equipped with a radiometric thermal camera and high-definition visual camera to perform an aerial thermography inspection over a solar PV system has become widely adopted. This practice has proved to be fast, safe, cost-effective, and highly accurate; providing a 95-99% accuracy rate in the detection of PV system anomalies and defects affecting performance. Aerial thermography is a versatile inspection application, its uses include inspecting 100% of PV modules during commissioning, annual maintenance, investigative inspections for PV system underperformance and to support warranty claims related to module performance and degradation, amongst several others.
Raptor Maps originally wrote this guide in October of 2017. This is an updated two-part version of the guide, as both the drone and solar industries and practices have evolved. This article discusses the precautions and steps that should be followed before inspecting a solar PV system to prevent any issues that would discredit the inspection data and reports. The following paragraphs cover pre-inspection planning and the onsite pre-flight checklist.
Pre-inspection Planning and Equipment Requirements
For aerial solar inspections and any drone inspections in the US, the drone pilot(s) will need to obtain their Part-107 ‘Remote Pilot Certificate’ license, read more about this here. Pilots must have a capable payload to begin inspecting PV systems with drones. Using the right equipment is the foundation of correctly performing an aerial solar PV inspection.
Equipment and Payload
The imaging system of a drone payload is the most important piece of equipment. A solar farm inspection requires a radiometric thermal camera, which can record the temperature of the solar modules and cells. Additionally, the camera must also capture the visual thermal imagery of each module. Best practices are to use a dual payload imaging system, which includes both IR and RGB lenses within the camera housing. Both the solar industry and Raptor Maps have standardized use of the 13mm thermal lens option but the 9 or 19mm lenses are also an option. The drone that carries the camera during the inspection should be an industrial-grade multi-rotor, such as the Matrice 200 series, or an enterprise-level fixed-wing, such as the senseFly eBee X.
Flight Planning Software
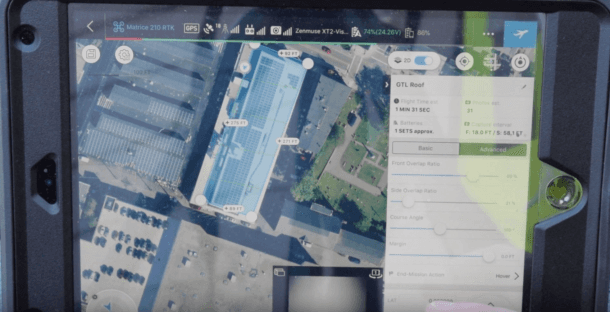
Flight planning software is crucial to correctly perform a drone solar farm inspection. Flight planning software needs to allow for adjustment of every flight variable and pilots should become accustomed to using the software to meet the flight and data requirements needed for data-processing and to create inspection reports. Raptor Maps has created standard flight guidelines and data requirements for pilots to use to perform a fast and efficient aerial thermography PV system inspection. Flight planning software helps the pilot set an automated flight path and image collection rate. This enables consistent and accurate imagery collection throughout the inspection. The type of inspection (warranty, commissioning, preventative maintenance, etc.) dictates the automated flight path and image collection rate. Raptor Maps has used its years of experience performing and supporting thousands of aerial solar inspections to create three levels of solar inspection and flight parameters.
Overview level inspections are high altitude and higher speed inspections that can identify large scale anomalies, with the smallest being malfunctioning modules.
Standard level inspections are flown at a lower altitude and speed than an Overview but can identify both large and small scale anomalies, from offline inverters to sub-module issues.
Comprehensive level inspections are flown to the IEC technical standards and are flown at the lowest altitude and speed of the three levels. This level provides highly detailed, granular sub-module level data, and absolute temperature accuracy of the strings and modules.
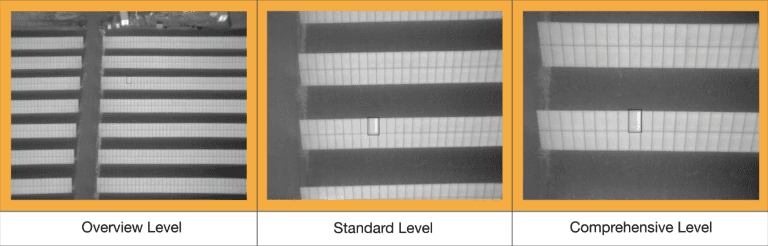
Depending on the level of inspection required for the project, the flight path software will enable the drone inspection to be performed correctly. Raptor Maps suggests DJI Ground Station Pro, DJI Pilot, or senseFly eMotion. Pix4Dcapture is another good option if pilots are already using this app. There are a variety of drone systems available today, read a list of supported hardware and payloads here.
Onsite Pre-flight Checklist
Environmental Conditions
Before beginning any drone inspection, the pilot(s) need to perform a detailed pre-flight checklist. The first thing to check before beginning any solar PV system drone inspection is the onsite environmental condition. High quality and accurate thermal data require specific weather conditions, including clear skies and sunny weather or a slight overcast at the worst. Irradiance level onsite needs to be greater than or equal to 600 watts/meter2. Raptor Maps recommends purchasing an irradiance meter and using it for every drone solar farm inspection to confirm sufficient irradiance. If the irradiance is not checked there will be a negative impact on the data’s quality. Also, humidity should be less than 60%, and the wind speed below 15 MPH (6.7 /s)m. Aerial solar PV inspections cannot be performed hours after a rainstorm onsite. The ideal time for aerial thermography solar inspections is in the middle of the day but can vary based on the location of the solar plant, time of year, and weather conditions.
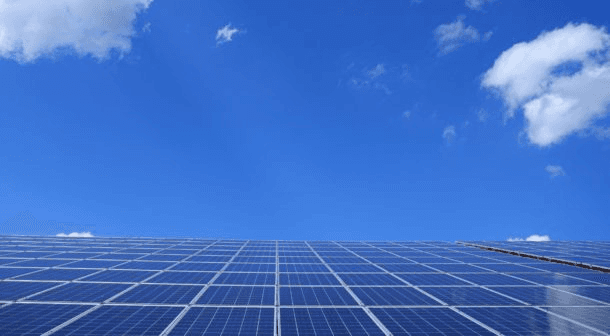
Energized Solar PV System
The PV system needs to be operating and energized during the drone inspection to collect accurate thermal data. Aerial thermography inspections can be performed throughout the year, even in the winter, but the window of time the inspection can be performed is much smaller several weeks before the summer solstice. For a more in-depth breakdown of the environmental conditions needed for a solar inspection, please watch episode 4 of the FLIR Systems and Raptor Maps webinar series “Thermal Drones and Solar Inspections”.
Conclusion
Pilots should ensure that these steps are carefully taken before beginning any drone solar PV inspection. Doing so will prevent the need for reflying due to poor or invalid data quality and wasted time on site which results in financial loss. In the second part of this blog series, the topics will cover best practices to follow during a solar PV aerial thermography inspection and a detailed post-inspection checklist, read part two here.
Next steps
From the civil engineering on your site down to the wiring on the back of your panels, the Raptor Solar platform provides you detailed, up-to-date data on the conditions and performance of your solar fleet so that your team has the intel they need to do their jobs effectively, quickly, and safely.